名古屋市から電車で1時間。愛知県南部に位置する碧南市は、大規模な臨海工業地帯を構える工業都市である。この街に本社を構える旭鉄工は1941年に創業した自動車部品メーカーで、トヨタ自動車(以下、トヨタ)の1次サプライヤーとして知られる。トヨタの部品メーカー団体、協豊会の構成メンバーでもあり、エンジン、サスペンション、トランスミッション、ボディなど幅広い部品を供給している。
2013年、この老舗メーカーにトヨタから転籍してきたのが木村氏だ。トヨタでは18年間技術部で製品開発に携わり、最後の3年間は生産調査部でトヨタ生産方式に則った改善活動に従事した。その知見を活かし、旭鉄工への転籍以降は徹底的にムダを省く改善を楽にする目的で工場のIoT(モノのインターネット)化に着手。地道な取り組みが実を結び、今では中小製造業のIoT成功事例として数多くのメディアで紹介されている。
2014年に始まったIoT化は、まさにDIY(Do It Yourself)を地で行くものだった。当初は市販のIoTシステム導入を検討したが、「あまりに高価、昭和の機械には適用できない、そもそもほしいデータが見えない」との理由から自作を決意。東京・秋葉原でセンサーを購入したり、小型PCのラズベリーパイを運用したりなどして費用を抑え、「可動率(べきどうりつ、機械設備を動かしたいときに正常に動かすことのできる割合)モニター」、「サイクルタイム(製品の工程開始から完了まで実際にかかる時間)モニター」を完成させた。
木村氏のモットーは、「人は付加価値の高い仕事をすべき」というものだ。それまでは人がストップウォッチを持ってこれらのデータを計測していたが、「アナログで取得するデータは散発的なものでサンプリングに過ぎません。旭鉄工はIoTによってデジタルでPDCAを高速化することができました」と語る。ただし、デジタルだけで改善活動は成立しない。こと製造業においてIoTが上手く行かない要因を、木村氏はこのように指摘する。
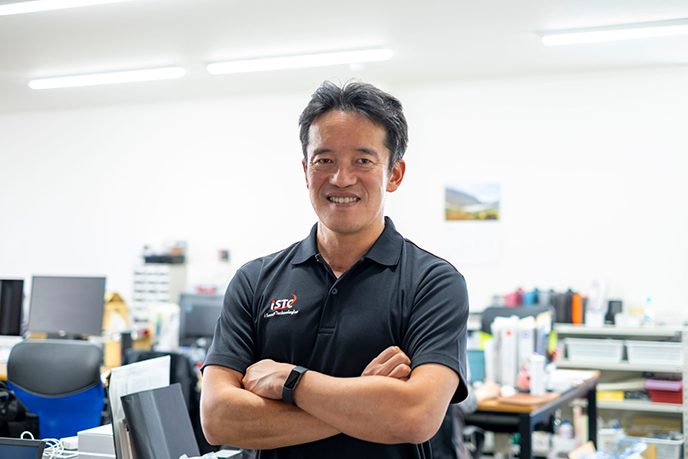
旭鉄工/i Smart Technologies(iSTC)代表取締役社長 木村哲也氏。旭鉄工は社員442名(2021年度)、iSTCは12名。iSTCは2名を除き旭鉄工からの出向者で、現場を知り尽くしたエンジニアが集結している(写真:小口正貴)
IoTは「問題の見える化」の手段
「IoTでは“数値の見える化”にこだわりがちですが、最も重要なのは“問題の見える化”です。我々はデジタルでいち早く問題をあぶり出し、表出した改善項目はあえて紙の『横展ボード』で現場に掲出して情報やノウハウを共有。現場の設備前で毎日決まった時間に『ラインストップミーティング』を実施して迅速に解決を図ります。そこまでやってようやく、0.01秒単位で時間が短縮されて効果が見えてくる。そして効果が見えてくると従業員の士気が高まり、カイゼンそのものが楽しくなってくるのです」(木村氏)