この連載について
基本要素を用いながら多面体形状の、より具体的な設計使用方法を解説する。また、主要な3D CADでの手法も併せて解説する。
- * 大塚商会では本稿で紹介している全ての製品を取り扱いしているわけではありません。
お客様のご希望製品の取り扱いがない場合もありますのであらかじめご了承ください。
【お知らせ】がんばる企業応援マガジン最新記事のご紹介
1.原点の基準をどこに設定するのが良いか?
3Dで新規に部品設計を開始する際、これまでの軸部品のモデリングを解説した連載において、3D空間に存在している原点およびXYZを基準にして部品形状を作成することが有効である旨を解説した。多面体の形状を作成する場合でも、基本的な考え方は全く同じである。
繰り返しとなるが、3D空間上に設定されている原点を基準としたXYZの3方向を示す仮想平面のうち、いずれかをスケッチ平面として使用して形状作成を開始する。その際にはこれから作成する部品の設計基準がどの位置にあるべきかを考慮することが重要である。
どこを基準とするかについて、多面体部品の場合は以下のいずれかのケースが考えられる。
- 加工の基準位置
- 相手部品に合わせた形状の部品:相手部品との組み立て基準位置
これも軸部品と同様、あくまで目安であり、100%きっちりと順守しなければならないというものではないので、使用していくうちにやりやすい方法が見えてきたら自分たちの中でのルールを確立すればよいであろう。
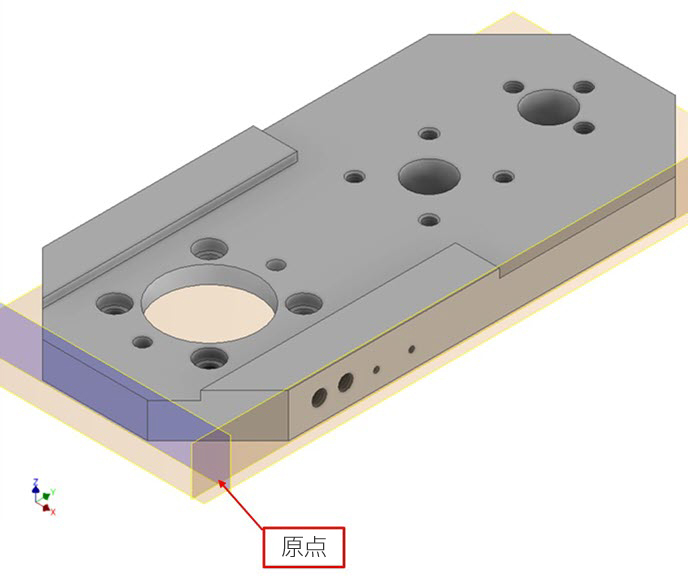
図-1 部品の手前側底面を原点に設定した例
2.多面体形状を設計する際のポイントは?
多面体形状のうち、6面体(立方体や直方体、以降角材と呼ぶ)は一般的にフライス盤で加工するため、6面を削る必要があることから円筒形状と比べて加工時間がかかり、サイズ公差や幾何特性の精度を上げることも難しいため、コスト高になる。
コストを少しでも下げるためにはさまざまな考え方があるが、代表的なものの一つとして使用する角材のサイズと、鋼材の面を削るためによく使用される正面フライスの直径との関係を考慮する方法がある。
角材の標準サイズは使用される材料ごとにJISで規定されており、これらを入手して加工することになる。また、市販の正面フライスのサイズはおおよそ種類が決まっている。
そこで、正面フライスの直径よりも少し小さめのサイズの角材を選ぶことで、工具が通るルート(工具パス)が最低限の動きで済み、コストダウンにつなげることができる。これは特に大きい部品において有効である。
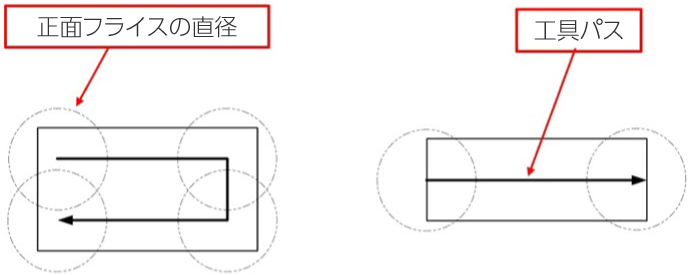
図-2 正面フライスの工具パス